NEW ENERGY TESTING SOLUTIONS
AUTHOR: Mr. Redzo Sakanovic
Head of Application & Integration
The GETEC e-mobility test benches were developed in cooperation with GTSystem, with the focus on the new challenges arising from the requirements for electrified or electric drive trains. In particular, the trend towards higher speeds in electric drives was taken into account in the design. We offer our customers a state-of-the-art test environment that is constantly being further developed.
With GETEC as a development partner, support from the engineering team is possible right from the start of the project.
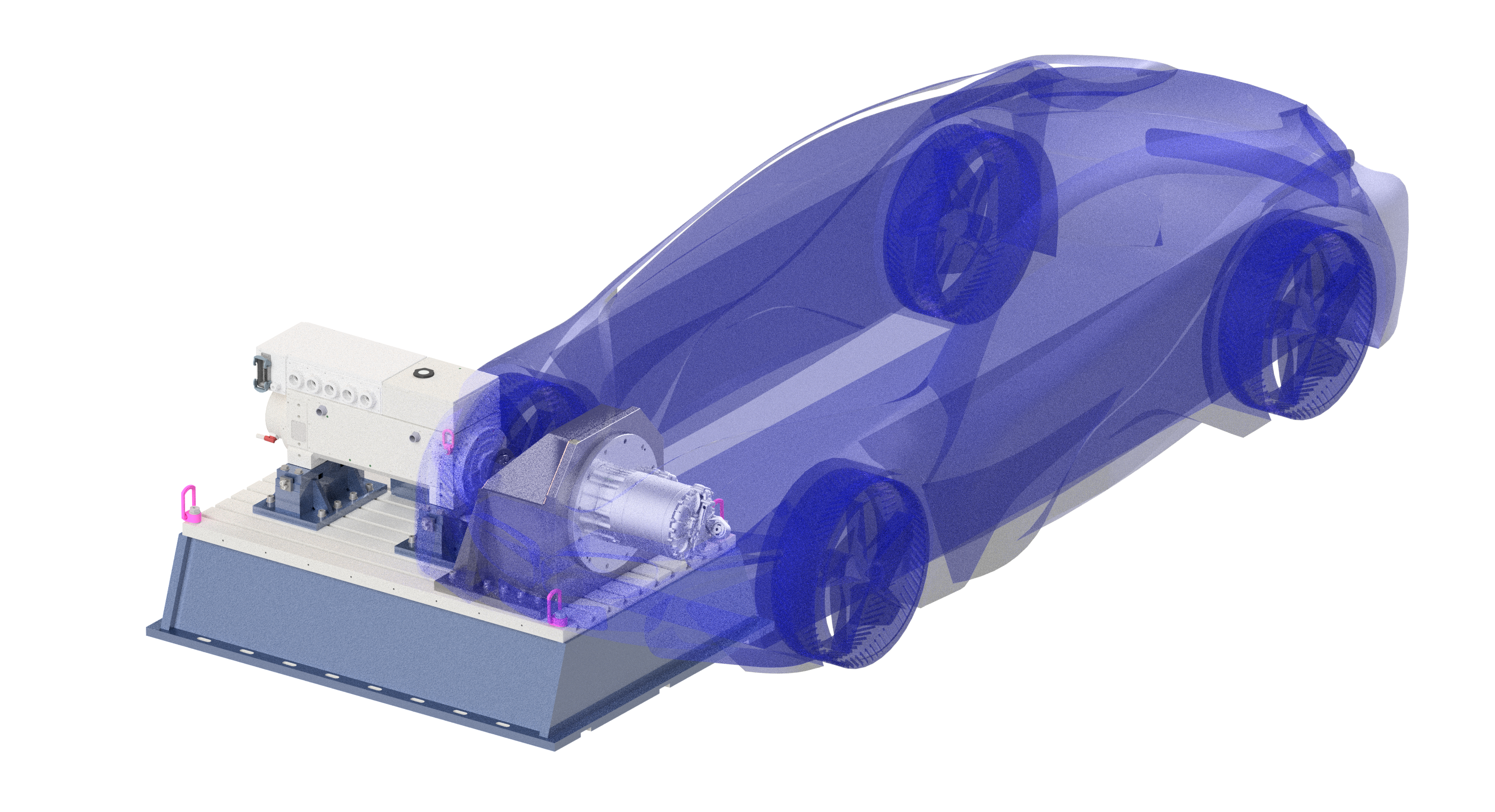
Fig. 4 | 1-Dyno bench (Simulating the drive motor)
The test environment is designed in such a way that customer requests can be reacted to extremely flexibly. Powertrains from (mild) hybrid applications (HEV), plug-in hybrids (PHEV) to battery electric vehicle drives (BEV) can be tested. The modern, state-of-the-art e-mobility test environment includes highly dynamic drive units that enable a speed range of up to 22,000 rpm and a torque of up to 700 Nm (see Figure 4).
Drive units with a performance range of 3,000 rpm and a torque of 3,500 Nm are available for testing the entire drive unit. A 2-dyno test bench is presented in Figure 5. The performance is simulated by the driven machines left and right.
If there is no drive motor or only the transmission for an electric drive is to be checked, a 3-dyno configuration is set up as shown in Figure 6. Here both the drive of the transmission and the output are simulated with test bench machines. In addition to this arrangement, a longitudinal arrangement can also be implemented.
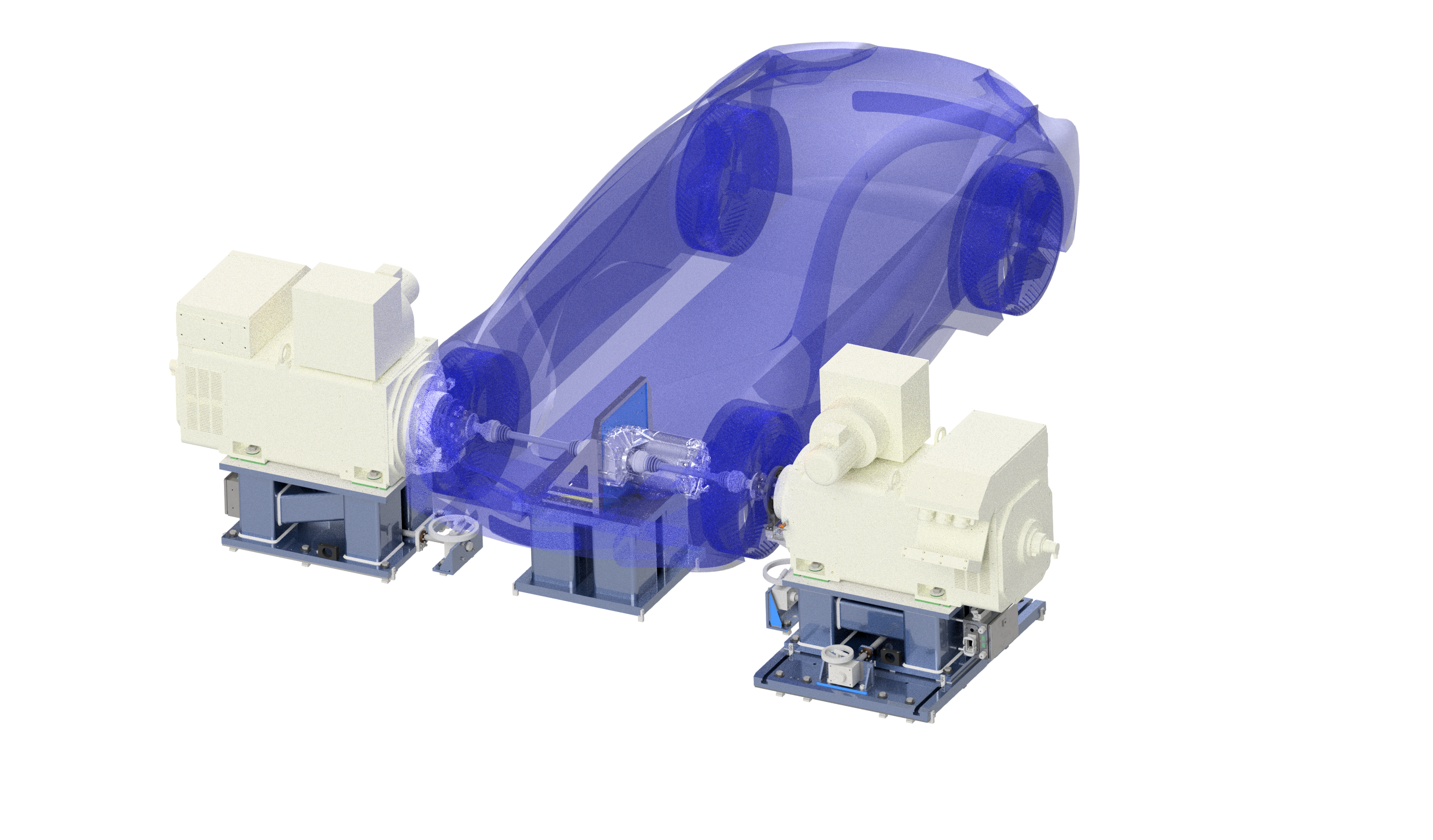
Figure 5 | 2-Dyno bench (Simulating the output)
Another important component is the simulation of different temperature environments. The cold and hot tests are also part of the LV123 test specification. The temperature simulation is implemented with a climatic chamber (-70 °C to 180 °C) and additional coolant conditioning (-30 °C to 130 °C). Due to this large configuration range, different variants of the test execution are possible:
- functional tests
- system checks
- security checks
- metrological services
The sensors used at GETEC are DAkkS-certified and comply with the deviation tolerances for speed, torque, current, voltage, pressure and temperature required in the specification.
Open communication with our customers is very important in order to achieve the jointly set goals in the specifications. In this way, the customer is informed ad hoc about the current test progress at all times. This enables the engineers to intervene in the development process and take countermeasures in the shortest possible time. In order to be able to optimally integrate the customer’s development engineers, various online support methods are available in order to be able to make program adjustments / adjustments in test processes in real time during commissioning.
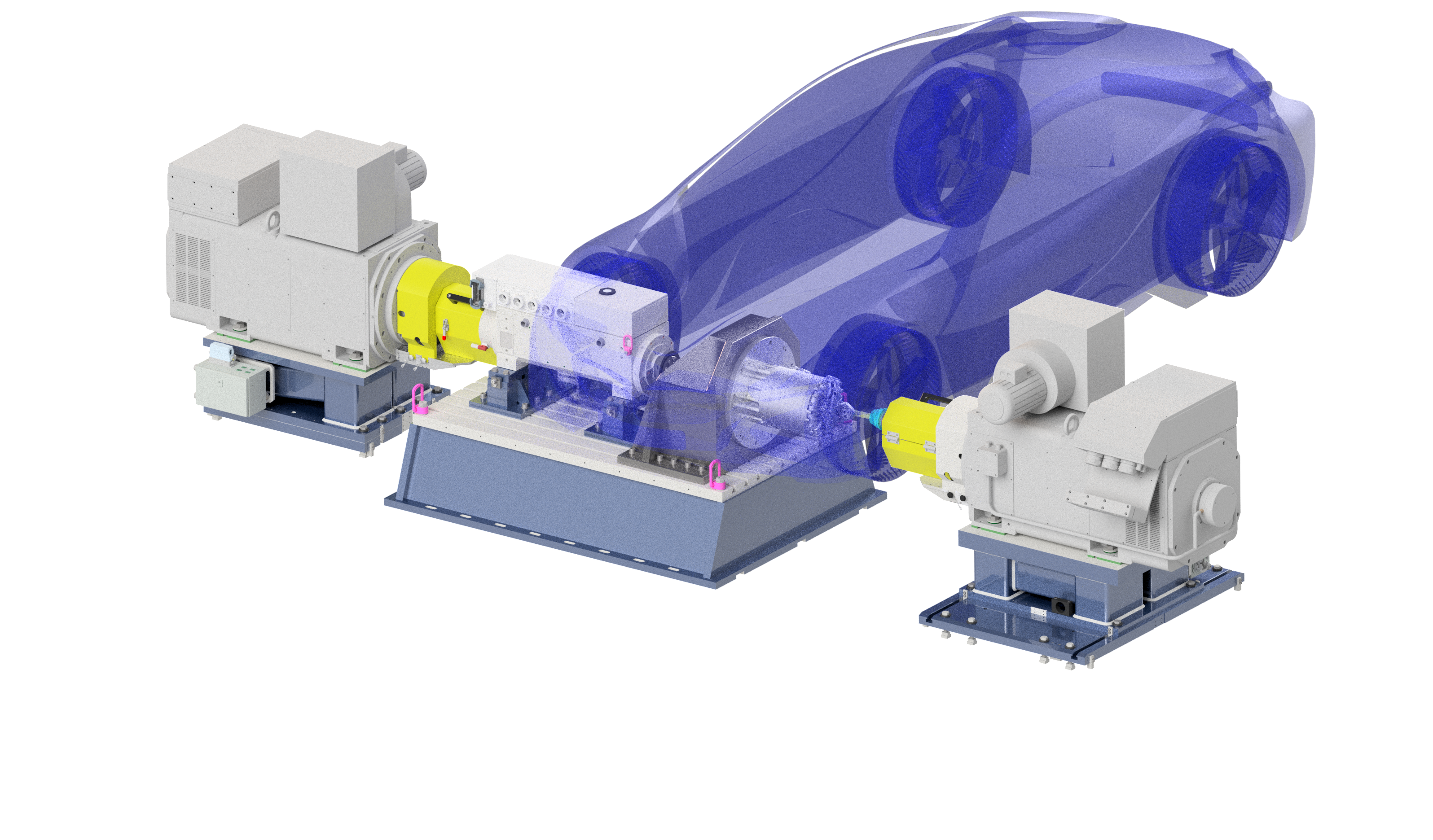
Fig. 6 | 3-Dyno bench (Simulating input and output)
For the first phase of the development of the electric motor (standalone), we can offer our customers an engineering service and control the electric motor via a development converter. With GETEC as a development partner, support from the engineering team is possible right from the start of the project.